Genflam® XLOH EFR (Enhanced Flame Retardant) Series are peroxide crosslinked thermoset jacket materials designed to provide the wire and cable industry with a low smoke non halogenated jacketing compound with faster curing option for improved production efficiencies, specifically for vulcanization utilizing the mold cure process. This series of compounds maintains a balance of excellent physical properties and ease of processing, and adds improved vertical flame performance in the overall cable design and meet the requirements of MIL‐24640B and MIL‐ 24643B military shipboard requirements.
KEY FEATURES
- Enhanced Flame Performance
- No Heavy Metals or Halogens
- Excellent Processing
- UV Stabilized
- RoHS and REACH Complaint
PHYSICAL PROPERTIES
Density: 1.50 g/cm3
Tensile: 1800 psi (typical)
Elongation: 200% (typical)
Tear: 45 lbf/in (typical)
Durometer: 96 Shore A
Low Temp. Brittle Point: ‐26ºC
Deformation, 2000g: <5%@121ºC
COMBUSTION PROPERTIES
Limited Oxygen Index (LOI): 38%
Smoke Index (ASTM E662): 0.2%
HEAT AGING
7d@136ºC | |||||
Tensile Retention |
105% |
|
|||
Elongation Retention | 78% | ||||
Hot Creep @ 200ºC | <10% | ||||
Hot Set @ 200ºC | 0% |
FLUID RESISTANCE
IRM 902 – 18h@121ºC | Diesel – 24h@100ºC | ||
Tensile Retention | 98% | 58% | |
Elongation Retention | 94% | 80% |
WEATHERING
720 Hours under QUV Testing |
|
Tensile Retention |
92% |
Elongation Retention |
87% |
SUGGESTED RUNNING CONDITIONS
Extruder L/D: 15:1 or 20:1
Comp. Ratio: 1.25:1
Screen Pack: 20 Mesh or none
Screw Type: Single Flight metering, without mixing section
Feed Zone: 190ºF
Center Zone: 190-200ºF
Head/Die: 220ºF
Conductor Pre-Hear: 150ºF (recommended)
PROCESSING TECHNIQUES
Genflam® XLOH EFR Series have been designed to process easily on standard extruders used in the production of wire and cable products. The material has been designed to process similar to elastomeric compounds, attaining maximum output levels at relatively low shear rates. Care should be taken to ensure that screw compression ratio levels are below 1.5:1, and flow restrictions in the crosshead are kept to a minimum. Melt temperatures higher than 230oF (110 oC) should be avoided.
The material can be extruded using either pressure or sleeving techniques. For maximum physical properties, tooling utilizing a slight draw down ratio (1.15 to 1) can be used. This series has been specifically designed for processes utilizing the mold cure method. Minimum mold cure temperatures of 230oF (110 oC) are recommended.
The material is supplied as free flowing pellets, packaged in sealed foil lined boxes and does not need to be dried prior to use. It is recommended that the foil liners be resealed after use to prevent outside contamination or water absorption during storage. If the material has been exposed to a high humidity environment, or the foil liner has not been sealed, it is recommended the material be dried for a minimum of 4 hours at 140oF (60 oC) in a standard desiccant style drier prior to use.
Similar products that might interest you
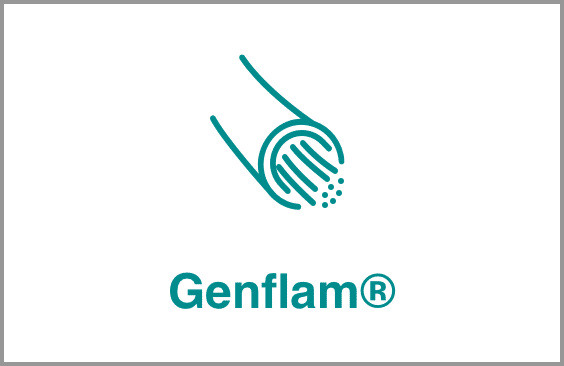
Genflam XLPO-2
This fast Peroxide Curing Thermoset Flame Retardant Low Smoke Zero Halogen Compound was designed to provide the wire and cable field with a flame resistant jacketing compound.
Learn More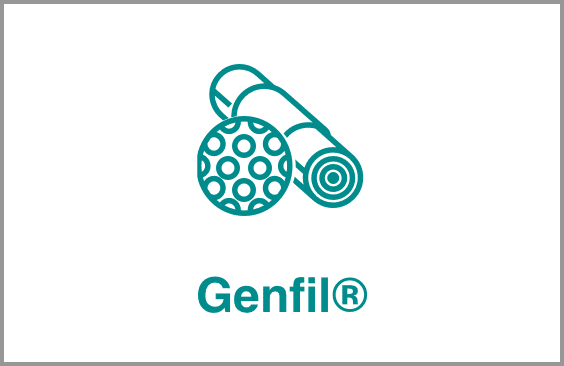
Genfil TP BC
A zero halogen flame retardant cable bedding compound that was designed as a moisture proof barrier and filler for use in Low Smoke Halogen Free (LZHF) constructions.
Learn More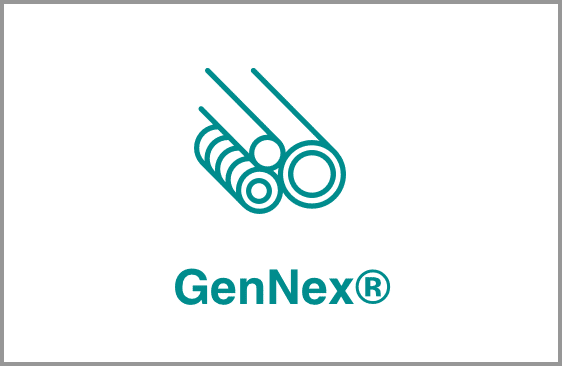
GenNex EU Ins
This compound has been designed to process easily on standard extruders used in the production of wire and cable products. The material is supplied as free flowing pellets.
Learn More