Genflam® XLMC‐H1 moisture cure compound is a 2 part system, the addition of 5 parts catalyst to 95 parts graft/FR will result in a jacket with excellent thermo‐oxidative stability, good fluid resistance and excellent physical properties. The material processes easily on standard extruders used in the production of wire and cable products; it will perform best on a mixing screw, with a low shear distributive mixing section.
KEY FEATURES
- Good processibility
- Excellent physical properties
- Excellent flame performance
PHYSICAL PROPERTIES
Density: 1.36 g/cm3
Tensile: 1900 psi (typical)
Elongation: 185% (typical)
100% Modulus: 1800 psi (typical)
Hot Creep @ 150ºC: 13.5%
Hot Set @ 150ºC: 1.2%
Low Temp. Brittle Point: ‐50ºC
COMBUSTION PROPERTIES
Limited Oxygen Index (LOI): 32%
HEAT AGING
7d@121ºC | 7d@158ºC | ||||
Tensile Retention |
112% |
91% |
|
||
Elongation Retention | 105% | 85% |
FLUID RESISTANCE
IRM 902 – 4h@100ºC | IRM 902 – 18h@121ºC | Diesel – 24h@49ºC | Diesel – 24h@100ºC | ||
Tensile Retention |
70% |
52% |
85% |
48% | |
Elongation Retention | 80% | 69% | 93% | 80% |
SUGGESTED RUNNING CONDITIONS
Extruder L/D: 20:1 or 24:1
Comp. Ratio: 1.25:1
Screen Pack: 20 Mesh or none
Screw Type:Mixing screw, with low shear distributive mixing section.
Feed Zone: 300ºF
Center Zone: 320ºF
Head/Die: 340ºF
Screw Cooling: Not recommended
Die Cooling: Not recommended
Gradient Cooling: Not recommended
Color Concentrate: PE Binder preferred
PROCESSING TECHNIQUES
Genflam® XLMC‐H1 moisture cure compound is a 2 part system, the addition of 5 parts catalyst to 95 parts graft/FR will result in a jacket with excellent thermo‐oxidative stability, good fluid resistance and excellent physical properties. The material will process easily on standard extruders used in the production of wire and cable products. It will perform best on a mixing screw, with a low shear distributive mixing section. Melt temperatures higher than 375ºF (190ºC) should be avoided.
It is supplied as free flowing pellets, packaged in sealed foil lined boxes and has a shelf life of 1 year when stored between 50‐85ºF (10‐30ºC) in its unopened, original packaging. Pre‐drying for 4 hours at 140ºF (60ºC) immediately prior to extrusion is recommended. The foil lined bags must be properly resealed between uses, as even short periods of storage in humid conditions may cause scorch during extrusion.
CROSSLINKING CONDITIONS
Genflam® XLMC‐H1 can be crosslinked by exposed to low pressure steam at temperatures up to 175ºF (80ºC). The time period may vary due to thickness of insulation, reel size and temperature.
Thickness | Time | Conditions | |||
0.5 mm |
4h |
165ºF (75ºC), 100% Humidity Sauna |
|
||
2 mm | 18h | 165ºF (75ºC), 100% Humidity Sauna |
Similar products that might interest you
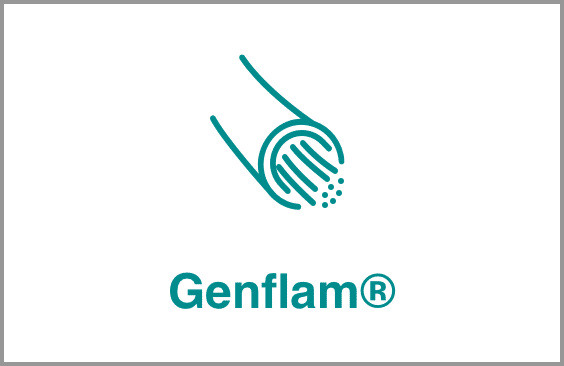
Genflam XLPO-2
This fast Peroxide Curing Thermoset Flame Retardant Low Smoke Zero Halogen Compound was designed to provide the wire and cable field with a flame resistant jacketing compound.
Learn More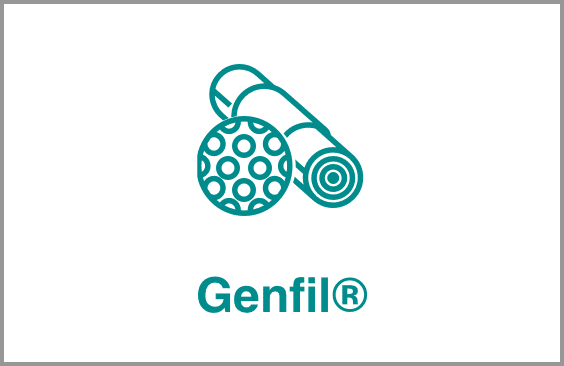
Genfil TP BC
A zero halogen flame retardant cable bedding compound that was designed as a moisture proof barrier and filler for use in Low Smoke Halogen Free (LZHF) constructions.
Learn More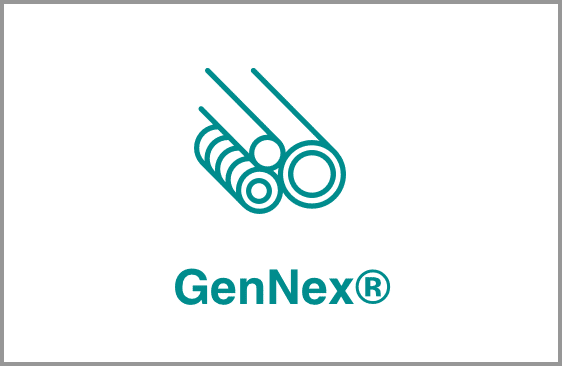
GenNex EU Ins
This compound has been designed to process easily on standard extruders used in the production of wire and cable products. The material is supplied as free flowing pellets.
Learn More